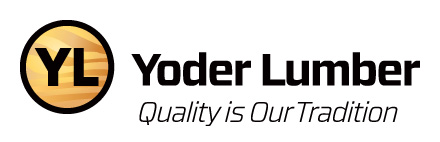
Yoder Lumber
Yoder Lumber, a third-generation family business, used Lucidchart to implement Six Sigma and deliver products faster to meet customer needs.
Key benefits
- DELIVER FASTER
- Yoder Lumber decided to use Lean Six Sigma principles to deliver high-quality products faster. They created process flow diagrams in Lucidchart to understand the current manufacturing process.
- OPTIMIZE PROCESSES
- As leadership worked together to reduce waste, they could highlight areas for improvement or make changes to the process flow diagram on the spot as people gave feedback.
- SIMPLIFY
- Once leadership made changes to the process, they shared the process flow diagrams with employees to add credibility to their findings and make sure employees understood what was expected of them.
- ENSURE SAFETY
- Yoder Lumber has also used Lucidchart to create decision trees (that they then print out and store in the safety handbook) that show employees how to respond to accidents in the workplace.
SIZE: Small (1-100 employees)
Over 70+ years, family-owned Yoder Lumber has grown from a five-person team with a portable sawmill into a corporation that manufactures and distributes Appalachian hardwood products in three different locations.
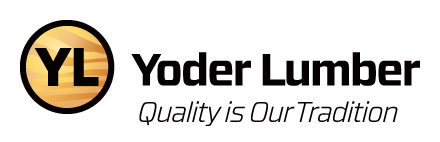
When it comes to the quality and speed that customers demand from manufacturers, retailers, and other businesses, the last 10 years have been revolutionary. Think about it—if you wanted to order a new toaster for your home, you can look through hundreds of options on Amazon until you find the model with every feature you need (stainless-steel surface, slots that fit bagels, etc.) in your preferred price range, and you can receive your order a mere two days later.
But these customer expectations don’t apply to just minor purchases on Amazon. They are impacting the manufacturing industry as well. Whether the order is big or small, manufacturers everywhere face a whole new set of standards as they strive to meet customer needs.
Over the last 70+ years, this Ohio-based company has grown from a five-person team with a portable sawmill into a corporation that manufactures Appalachian hardwood products in three different locations. CPO Tony Yoder explained that it’s been difficult to satisfy customer needs, especially since the company expanded internationally: “Customers are getting much more specific about what they want and what they need. It’s up to us to provide them with real solutions to their problems.”
A lot of Yoder Lumber clients use the just-in-time methodology, where companies aim to increase efficiency and lower inventory costs by receiving goods only as they need them within the production process. So not only do Tony and his team need to provide items that match a client’s specifications, but they need to deliver them quickly. Where Yoder Lumber used to have a two- to three-week lead time, they now only have a few days in some cases to deliver the requested products.
Discovering the Lean Six Sigma method
How can you effectively meet customer needs—both in speed and quality?
Yoder Lumber decided to implement a Lean Six Sigma program. For those less familiar, this methodology combines elements from Lean manufacturing and Six Sigma to streamline processes by eliminating eight types of waste, including defects, overproduction, and waiting between steps. Yoder Lumber brought in outside consultants to set up the groundwork, but afterward, they ran into two main challenges:
- Application: Lean manufacturing can seem like a lofty vision at first, and the reality of implementing it will means different changes for different companies. How would Yoder Lumber actually apply this methodology in their workflows?
- Training and implementation: Even once they nailed down an updated process, Yoder Lumber knew they would need to explain these changes to employees who may not understand these abstract ideas or buy into the new process quickly.
Spoiler alert: These challenges weren’t challenges for long once Yoder Lumber turned to Lucidchart.
Our visual productivity platform has helped this third-generation family business visualize processes to ultimately deliver the high-quality goods they have promised customers.
Visualizing the process to apply Lean principles
For Tony Yoder, what enables someone to succeed in an operations role is “knowing the process that it takes to produce the product comprehensively.” This qualification becomes essential in Lean Six Sigma—you have to know the strengths and failings of the current process to make strategic changes.
Lucidchart gives the team at Yoder Lumber an opportunity to better understand their manufacturing process. Tony elaborates:
“I like Lucidchart a lot for process flow diagrams to look at the steps that it takes to do something, in particular, manufacturing, and get that in front of everyone. It helps us go through it step by step and create some discussion around it.”
Ryan Yoder, Procurement and Logging Operations Manager, had already been drawing out his thoughts on paper or on whiteboards. Lucidchart simply gave him an easier way to share those visualizations and edit them:
“You never get the process right the first time. When I started using Lucidchart, you can just move stuff around so easily. If I create a process flow diagram, I’ll put a rough one together, and then I’ll get a group together and go over it. The process of actually creating the diagrams as a group forces us to think through the process as we’re doing it.”
Both Tony and Ryan expressed that diagramming processes is a group effort, and Lucidchart’s features make it easy for teams to collaborate. Tony and Ryan pull up the process flow on a projector or laptop and make changes on the spot as team members give feedback—changes that are automatically saved to the living diagram everyone references.
Ryan shares how, once they map the process, instances of waste become more apparent: “That’s where Lucidchart comes in handy. I can see a bottleneck pretty clearly. Once you identify the true pain point of a process, it’s usually not hard to find ways to improve that. Basically, we’ll break it down into steps and a to-do list and work through that.”
The process doesn’t end after Yoder Lumber finishes that to-do list. The Lean Six Sigma methodology requires businesses to continuously monitor their processes and see where they can make other improvements. Tony explains, however, that Lucidchart helped Yoder Lumber through continuous improvement as well:
“I’ve used it to look at the process cycle time. Certain types of processes take a long time, and I’ve been labeling those up alongside the process. It’s helped us as far as adding up all the individual process times and getting that data. Then, you can see if you change this or reduce the time to do this and how big of an effect it has on the process.”
Simplifying the abstract for the entire team
If you remember, there’s another significant challenge when switching to Lean Six Sigma: training and implementation. Yoder Lumber found places where they could streamline the manufacturing process, but then they had to make these complex processes accessible for employees performing the work, especially in a community that’s not as technology-focused.
Tony explains that this is where the process flow diagrams created earlier come in handy again: “To be able to take a more abstract idea and be able to make it a visual for people makes a pretty significant difference.”
Lean Six Sigma doesn’t go anywhere if employees don’t adapt. When employees understand the process the first time around, they can start cutting waste and production times right away.
The process flow diagrams created in Lucidchart also increase buy-in from employees, first because they enable leadership to work quickly and prove the success of the Lean Six Sigma program and second because they add credibility. Ryan and Tony elaborated:
“Lucidchart diagrams make a nicer presentation. It makes it easy to show to other people, to convince other people. If it’s not cobbled together, it’s a lot easier to sell the idea.”
Tony and Ryan mentioned that, in particular, automatic alignment and the extensive template library available in Lucidchart have made it easy to present something professional without much effort or training.
Ensuring the safety of the team
And the benefits of Lucidchart don’t stop there.
Aside from Lean Six Sigma processes, Tony Yoder has used Lucidchart with his safety coordinator to build out documentation for how to respond to accidents in the workplace. Most productivity apps save companies money, but what if one can save lives—or at least make sure the injured employee gets to the doctor safely?
Similar to the process flow diagrams, decision trees clearly show the steps one should take if an accident happens on site so the employee can respond quickly. Tony created the decision trees in Lucidchart, published them, and added them to the company’s safety handbook, in hopes that visuals would help employees retain this important safety information and quickly follow procedure: “It’s a good way for people to review every now and then. They can use this to remember how to react when something happens.”
With Lucidchart, Yoder Lumber visualizes various parts of the manufacturing process to make work better for employees and guarantee high-quality products for consumers. Whether you’re part of a growing, family-owned business or a corporation that spans the globe, whether you strictly adhere to Lean Six Sigma or prefer your own methods, our platform has a solution for you.